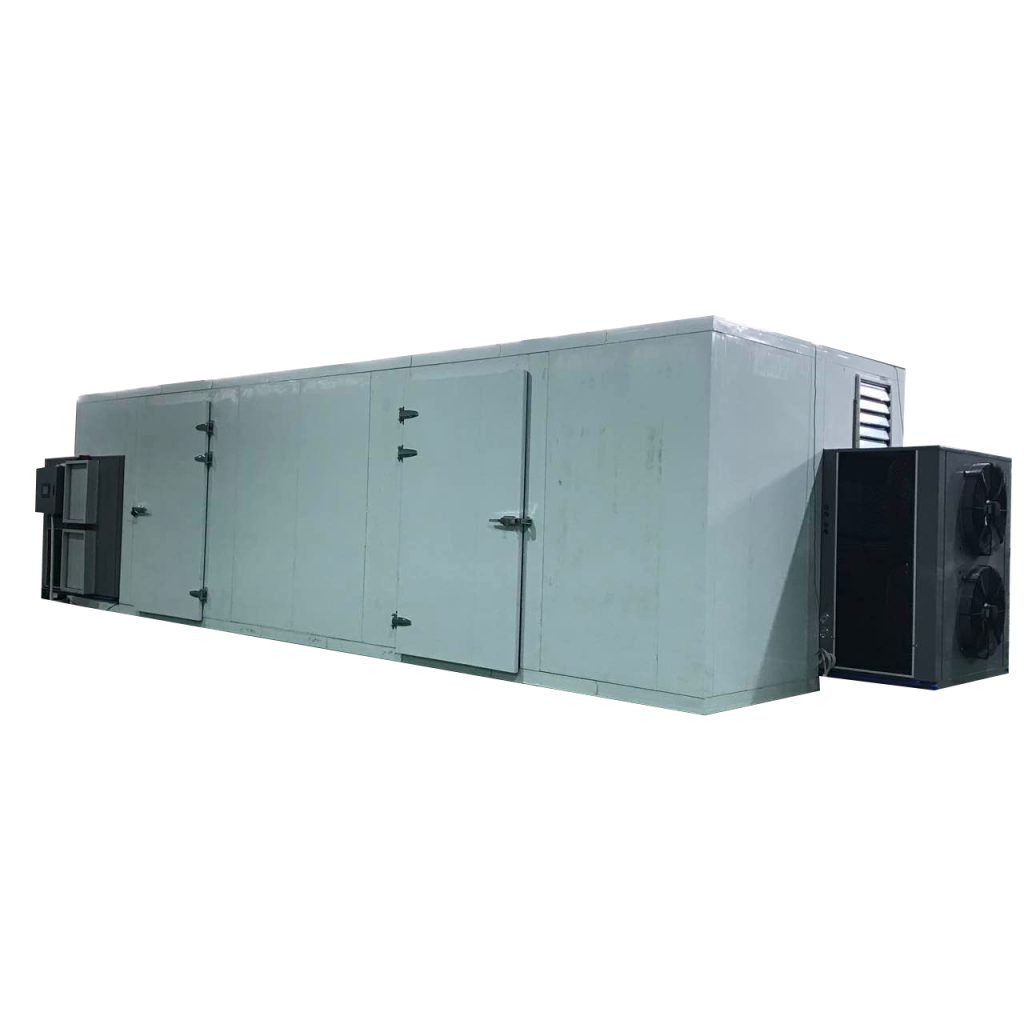
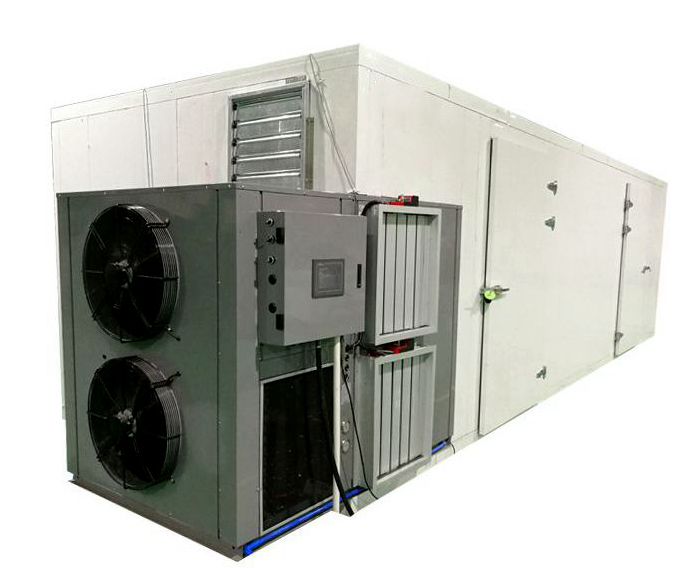
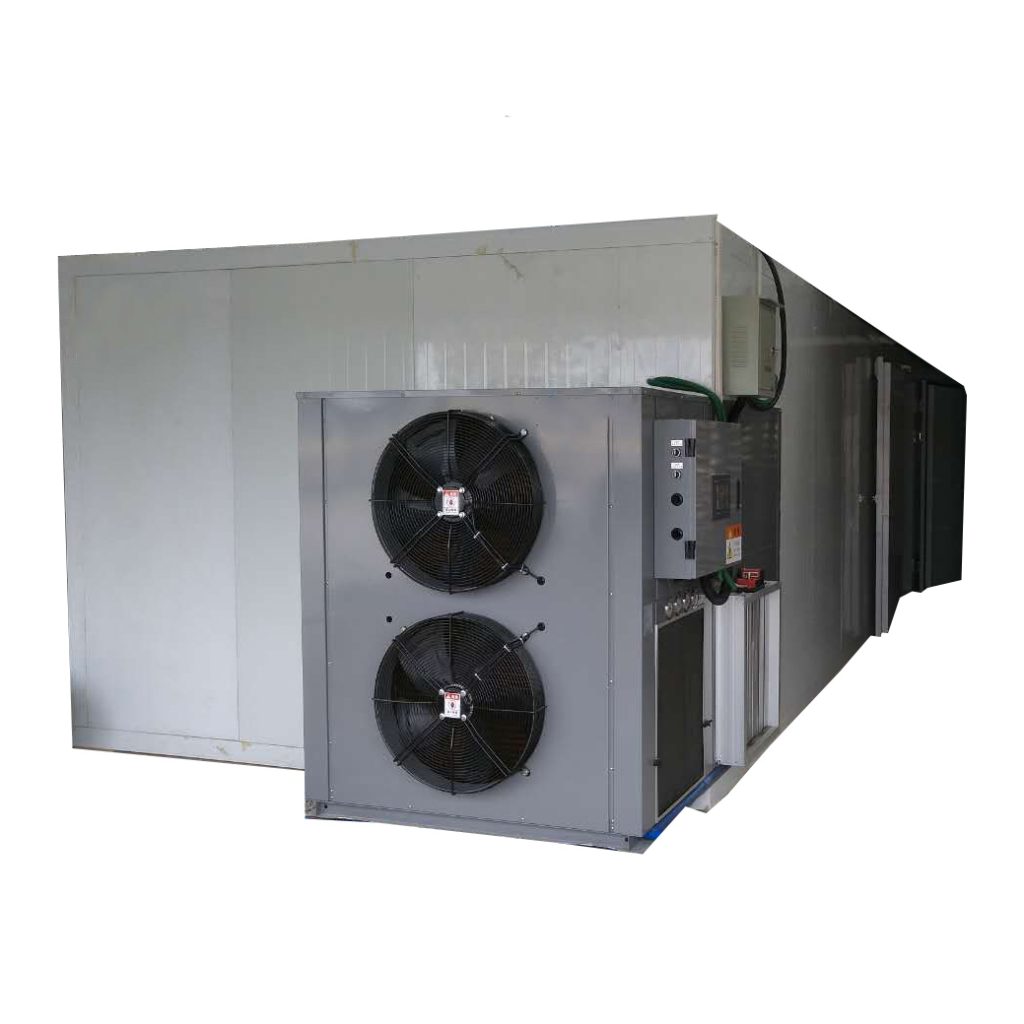
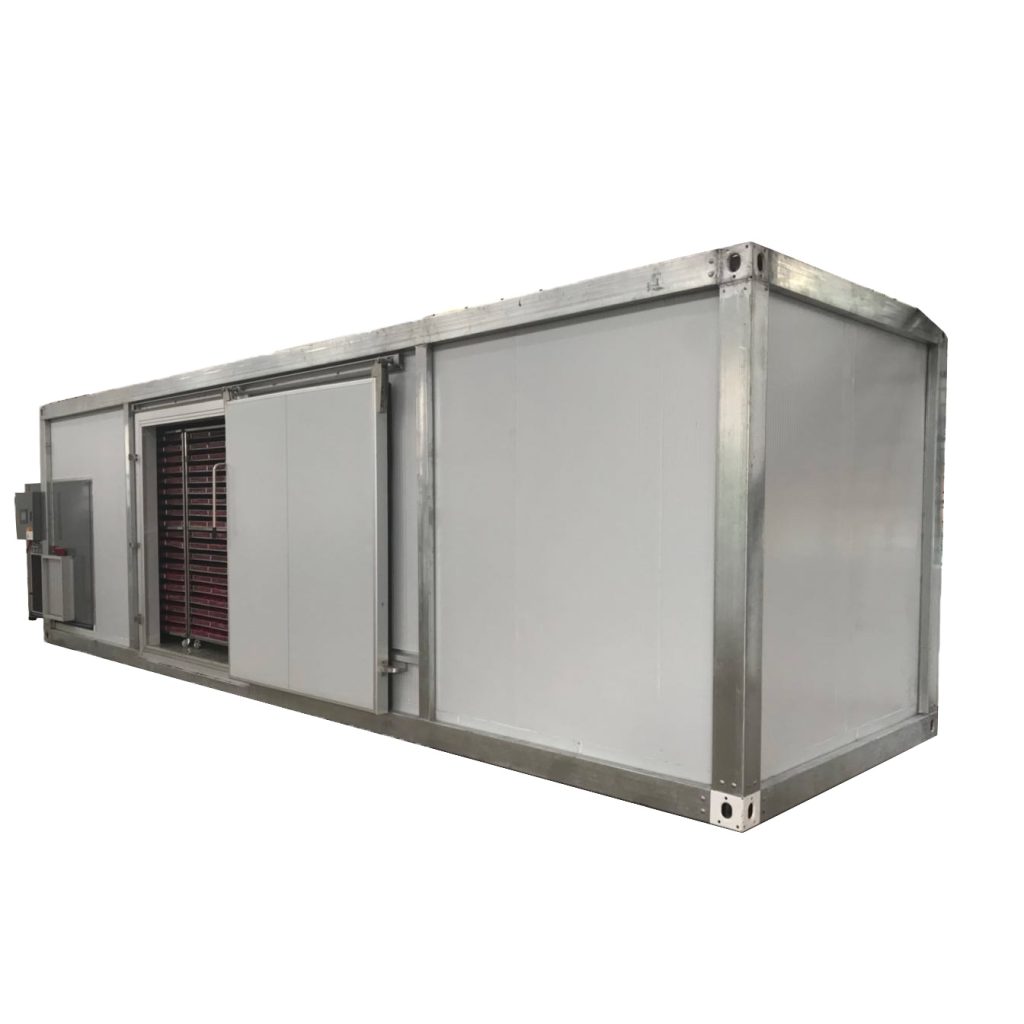
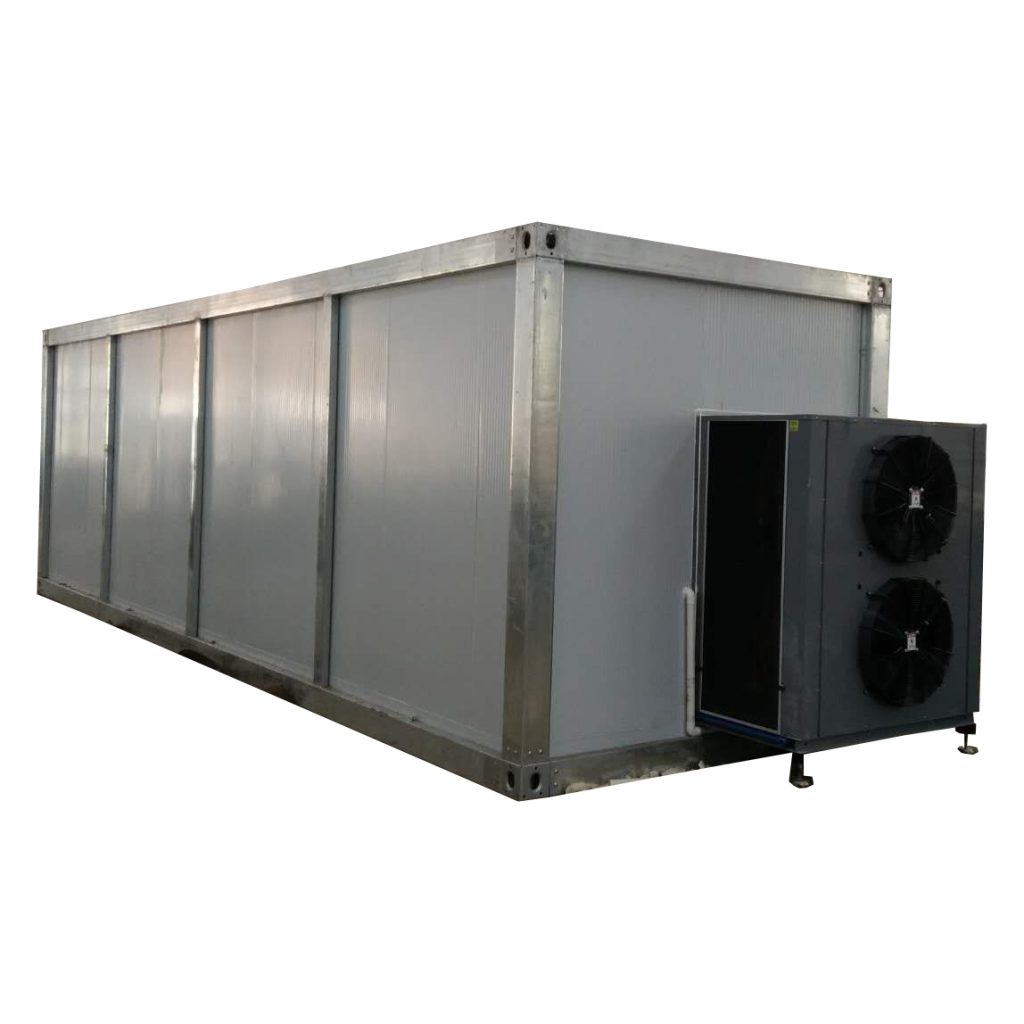
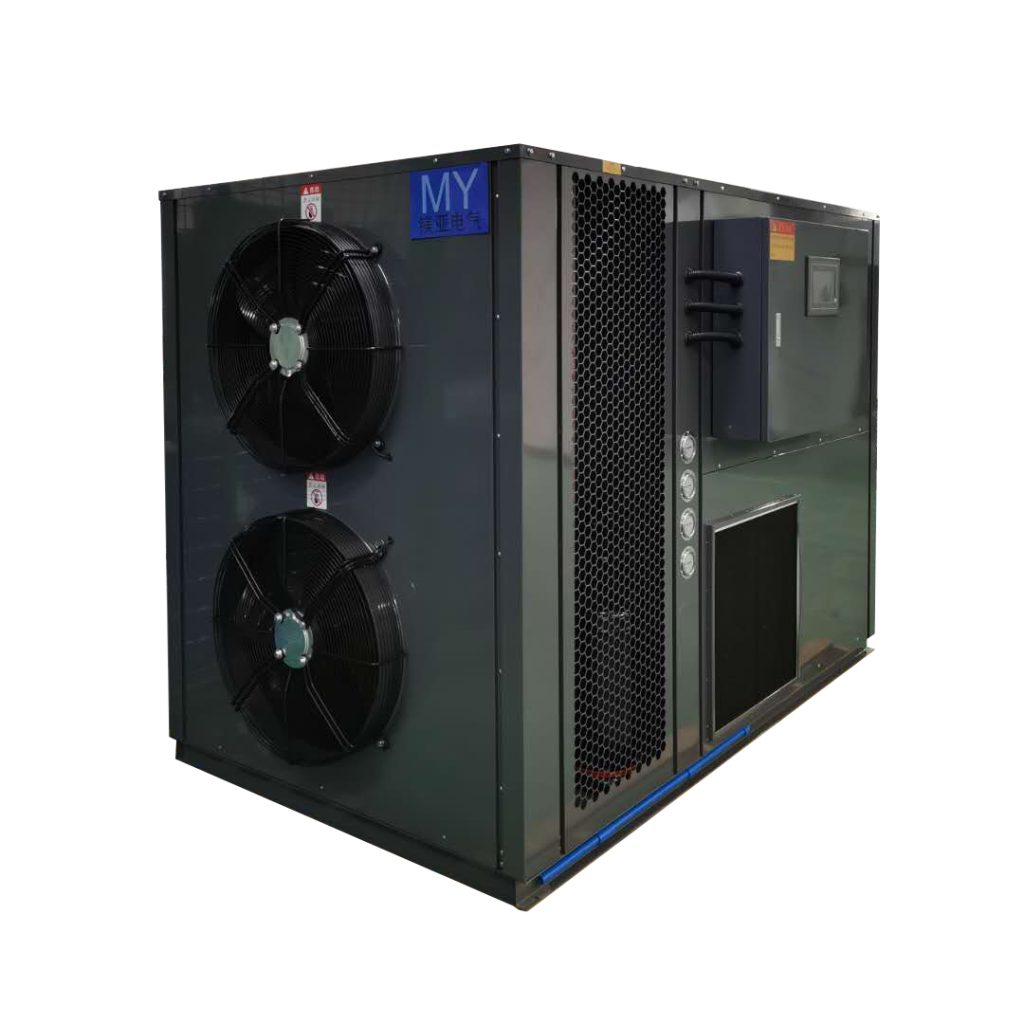
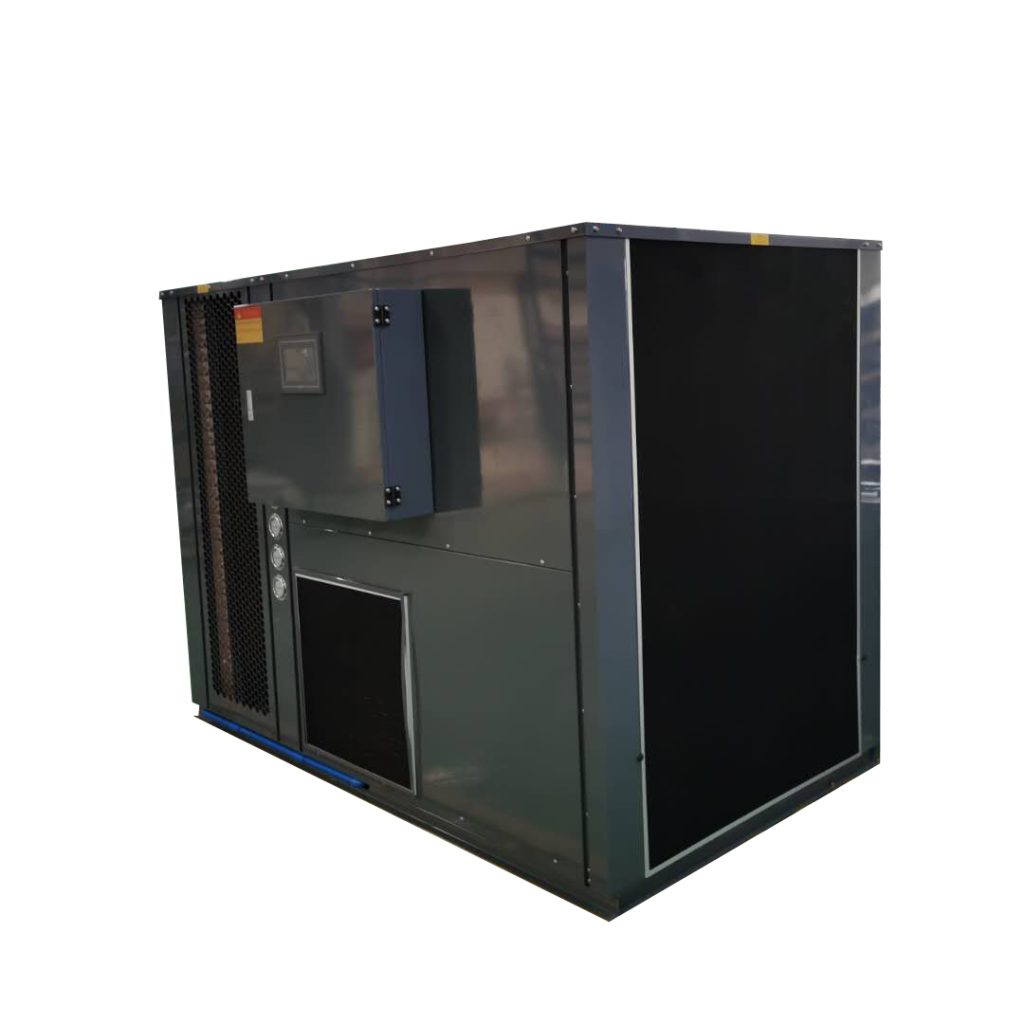
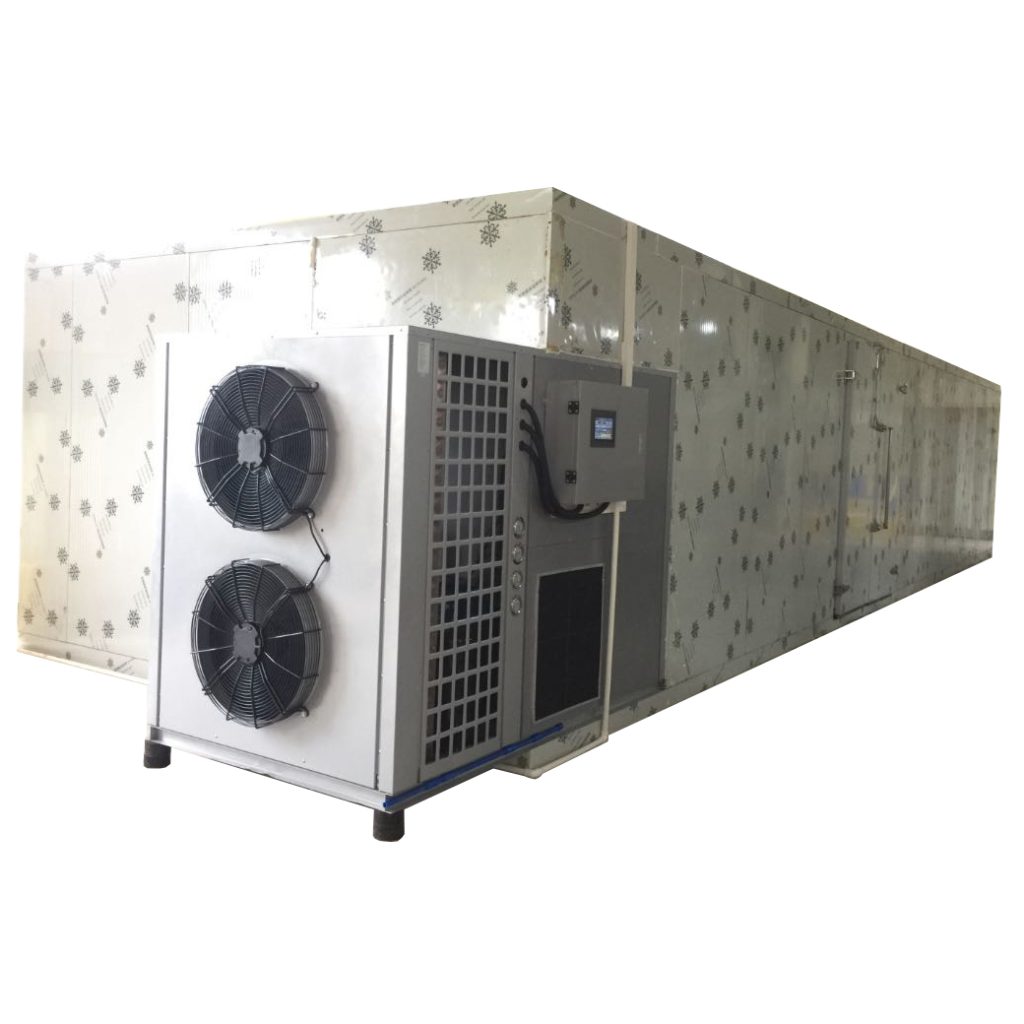
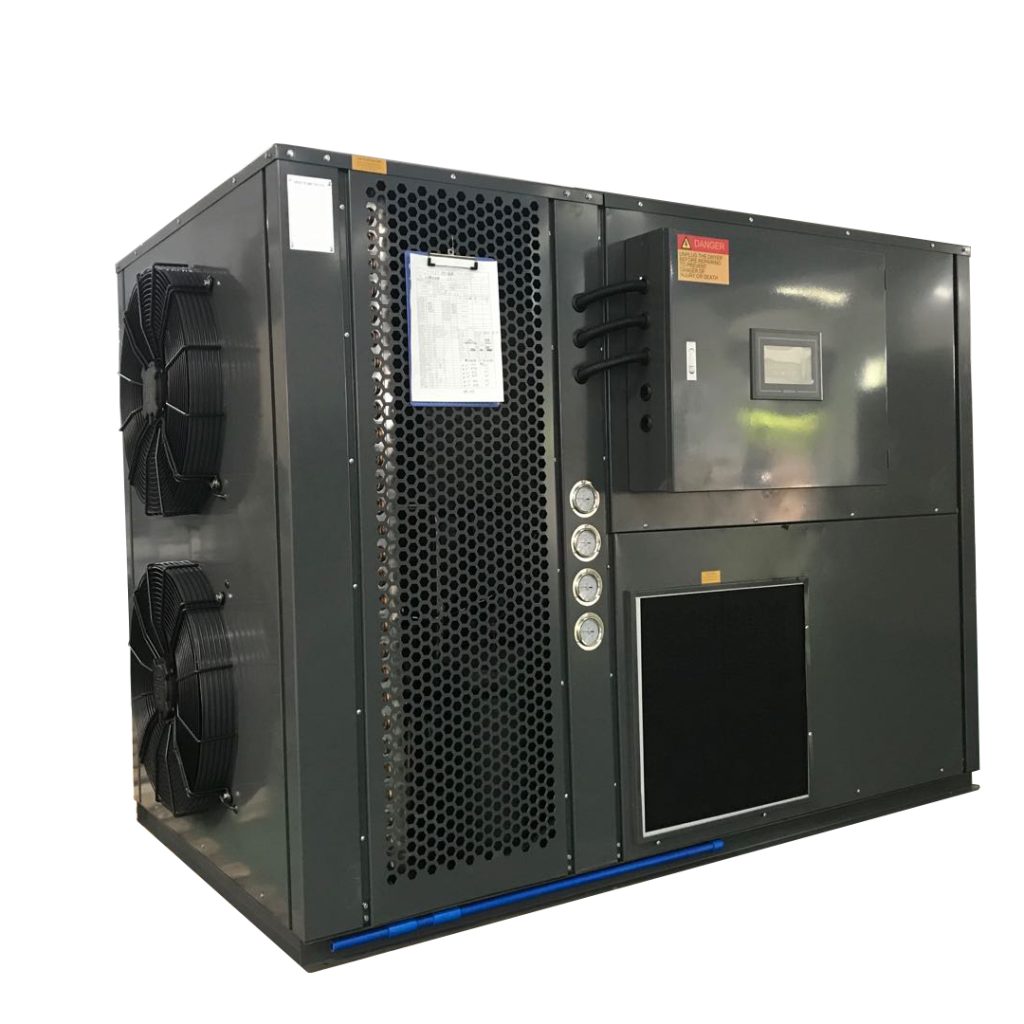
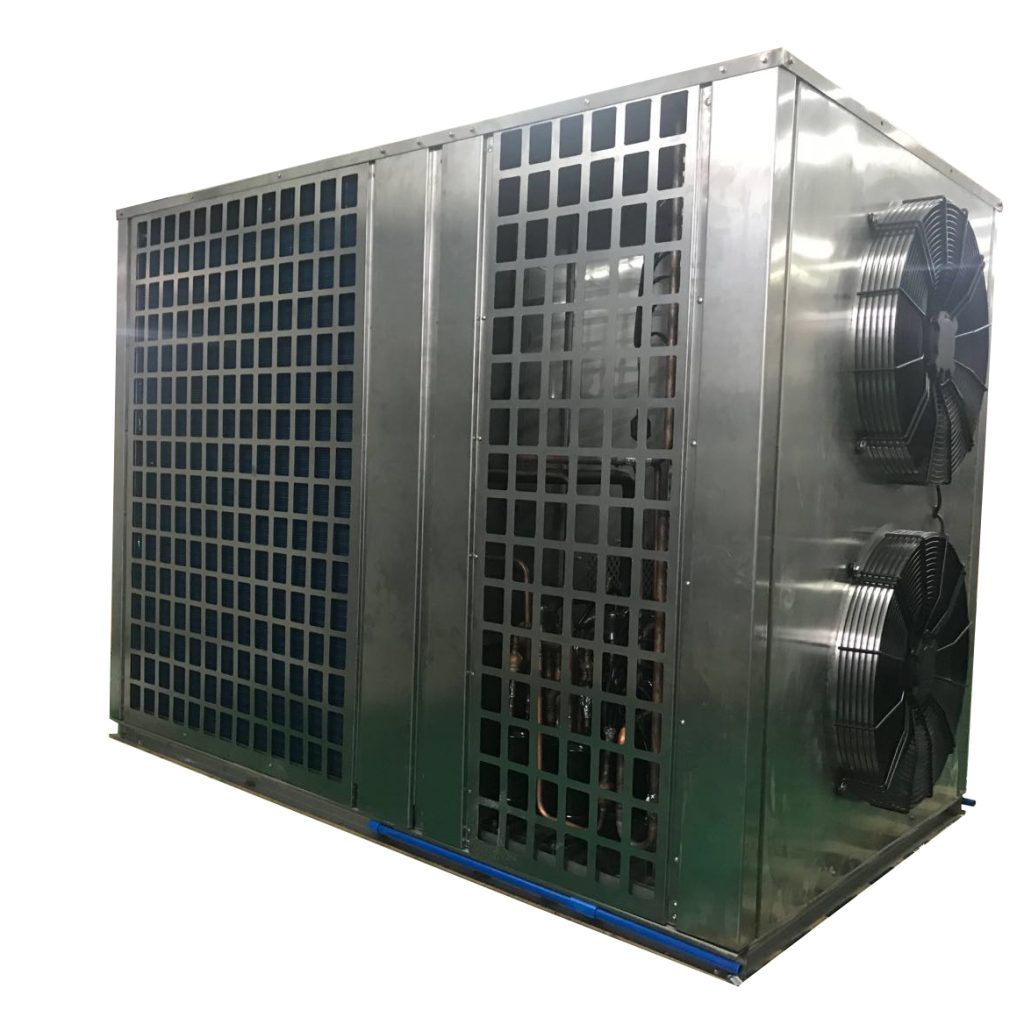
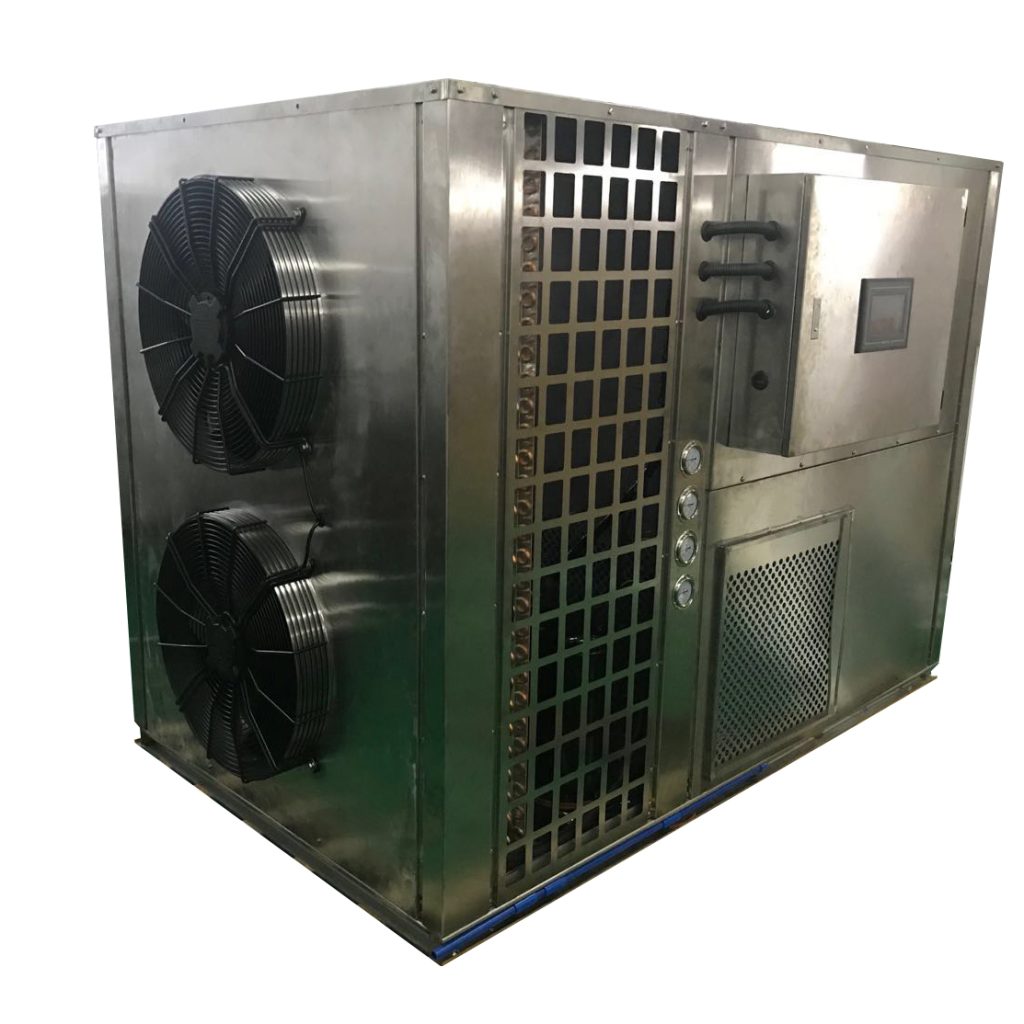
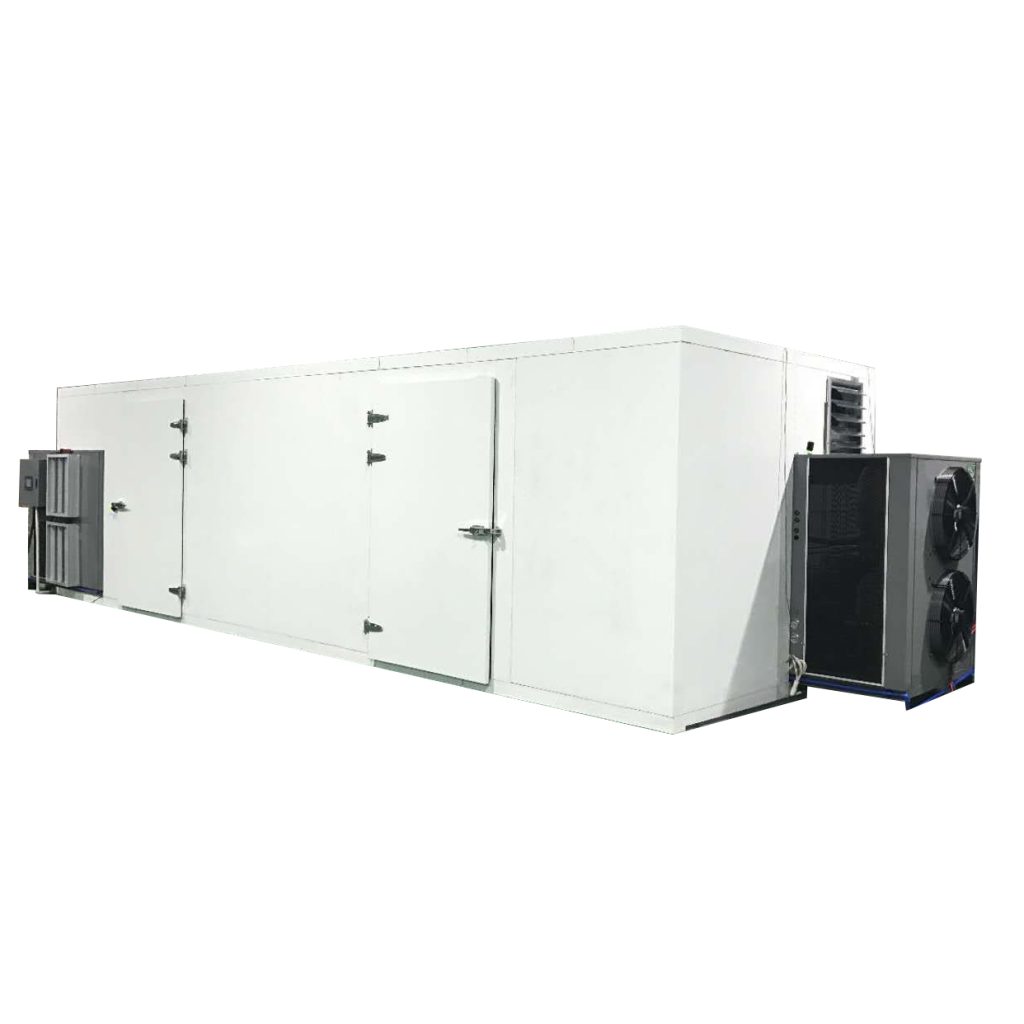
Transform your food processing operations with the MeiYa Commercial-Grade Energy-Saving Dehydrator—an advanced, multi-functional drying solution designed to handle diverse products like fruits, fish, apricots, herbs, and more. Engineered for industrial-scale efficiency and sustainability, MeiYa’s dehydrator combines cutting-edge heat pump technology with intelligent automation, delivering premium quality while slashing energy costs by up to 70%.
Key Features of MeiYa Energy-Saving Dehydrator
- Multi-Food Drying Capability
MeiYa’s system excels in dehydrating a wide range of foods, including delicate fruits (apricots, figs), protein-rich fish (salmon, shrimp), leafy herbs (honeysuckle, tea leaves), and even tobacco or hemp. Its customizable trays and adjustable shelving accommodate varying sizes and textures, ensuring optimal airflow for uniform drying. - Energy-Saving Heat Pump Technology
Utilizing heat recovery mechanisms and a low-temperature drying range (30°C–80°C), MeiYa reduces energy consumption by recycling thermal energy during operation. With a power input of 19.4kW, it achieves rapid heat-up times while maintaining a carbon-neutral footprint. - Stainless Steel Construction & Hygienic Design
Built with food-grade stainless steel chambers and 50mm polyurethane insulation, the dehydrator resists corrosion and contamination. Seamless surfaces and easy-to-clean components comply with HACCP and CE standards, making it ideal for sensitive products like seafood and organic produce. - Automated Operation & Precision Control
A user-friendly touchscreen interface allows operators to program drying cycles, monitor humidity, and adjust wind volume for tailored results. Real-time fault diagnostics and 24/7 unattended operation minimize downtime in high-volume facilities. - Scalable Solutions for Diverse Needs
Choose from batch capacities of 300kg to 3500kg, with modular configurations supporting up to 1152 trays. Customizable accessories (e.g., stainless steel hooks, shelving) adapt to unique requirements, whether drying apricots for export or preparing smoked fish for retail.
Why Choose MeiYa?
- Cost Efficiency: Reduce annual energy bills by 40-60% compared to traditional dryers.
- Global Compliance: Compatible with 380V/50Hz/60Hz power supplies and certified for international markets.
- 12 Months Warranty: Backed by reliable after-sales support and maintenance services.
Applications
- Fruit Processing: Preserve apricots, mangoes, and berries with retained color and nutrients.
- Seafood Dehydration: Prepare dried fish, shrimp, and squid for snacks or culinary ingredients.
- Herbs & Spices: Dry tea leaves, medicinal herbs, and spices without losing potency.
- Customized Projects: Collaborate with MeiYa’s engineering team for tailored drying systems.
Upgrade to MeiYa—Where Innovation Drives Sustainability
Elevate your food production with a dehydrator that balances precision, efficiency, and eco-friendliness. Ideal for food processors, export businesses, and agricultural cooperatives aiming to scale operations sustainably.
Contact us today for a customized quote or to explore batch testing!
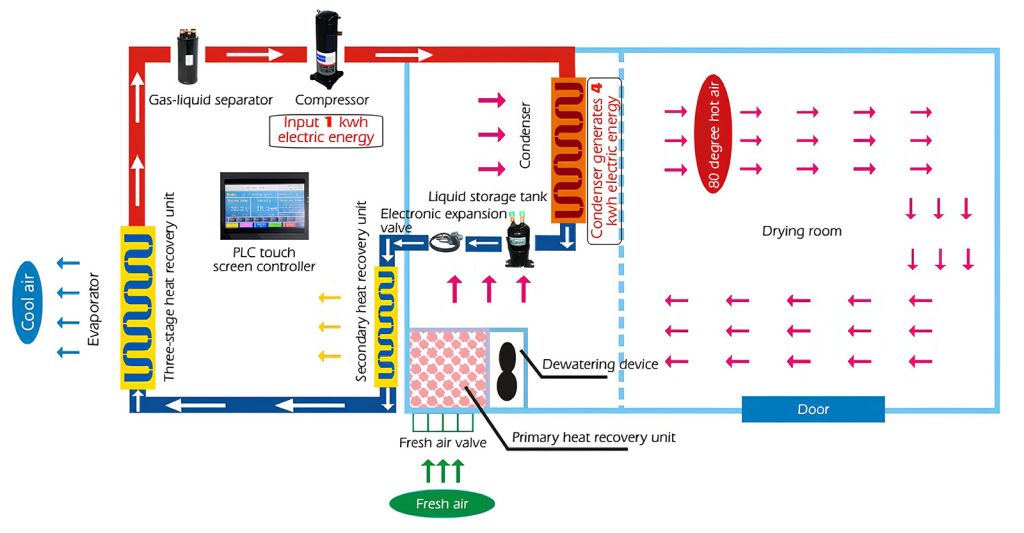
MeiYa Heat Pump Dryer Machine
- No MOQ & Customization Unlimited
- Drying + Dehumidify + Cooling
- PLC + Touch Screen Control
- 7-10 Days Delivery Time
Parameter:
Single dryer+drying chamber | ||||
Model | Unit | MY-03RD | MY-06RD | MY-12RD |
Power input | KW | 5.5 | 9.5 | 19.4 |
power supply | V/PH/HZ | 380V/3PH,50/60HZ | 380V/3PH,50/60HZ | |
220V/1PH,50/60HZ | ||||
Rated current | A | 9.6A(380V),22A(220V) | 17.0 | 30.0 |
Heating capacity | KW | 10.5 | 21.0 | 42.0 |
Cooling capacity | KW | 7.8 | 18.0 | 32.0 |
Dehumidity | L/H | 12.0 | 25.0 | 50.0 |
Max temperature | ℃ | ≤75 | ≤75 | ≤75 |
Working condition | ℃ | 0-43 | 0-43 | 0-43 |
Electric shock protection grade | 1 | 1 | 1 | |
Max exhause pressure | M(P)a | 30 | 30 | 30 |
Noise | d(B(A | 75 | 75 | 75 |
Power consumption/H | KWH | 4.8 | 8.5 | 15.0 |
Electric heater | KW | 3.0 | 6.0 | 12.0 |
Blowing type | / | HORIZONTAL BLOWING TYPE | ||
Demsnssion of dryer | MM | 1650*856*1280 | 1806*1065*1280 | 2089*1260*1580 |
Weight | KG | 180 | 285 | 480 |
Buying Guiding:
Recommend drying machine+Drying chamber sizes
ITEM | DESCRIPTION | PRODUCT CAPACITY | DRYING CHAMBER SIZE |
1 | One unit MY-03RD+Drying chamer | (300-600)kg/batch | 3200*2190*2200 (mm) |
2 | One unit MY-06RD+Drying chamer | (600-1000)kg/batch | 6150*2190*2200 (mm) |
3 | One unit MY-12RD+Drying chamer | (1200-2500)kg/batch | 6350*3230*2200 (mm) |
4 | One unit MY-15RD+Drying chamer | (1300-2800)kg/batch | 6350*3230*2200 (mm) |
5 | Two unit MY-03RD+Drying chamer | (1200-2000)kg/batch | 7050*2190*2200 (mm) |
6 | Two unit MY-06RD+Drying chamer | (1500-2500)kg/batch | 10100*2190*2200 (mm) |
7 | Two unit MY-12RD+Drying chamer | (3500-5000)kg/batch | 11860*3230*2200 (mm) |
8 | Two unit MY-15RD+Drying chamer | (4000-5500)kg/batch | 11860*3230*2200 (mm) |
Our Projects:
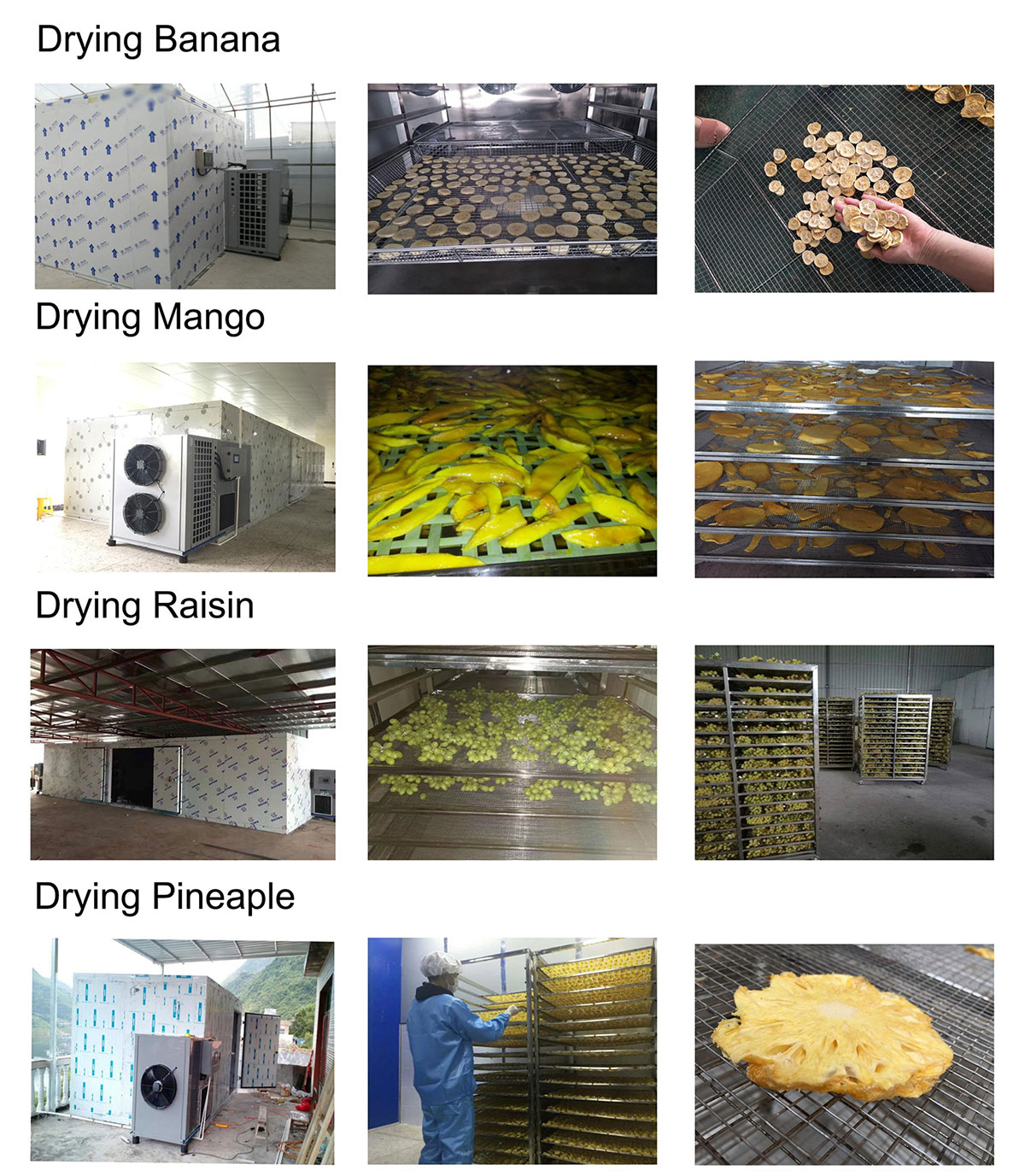
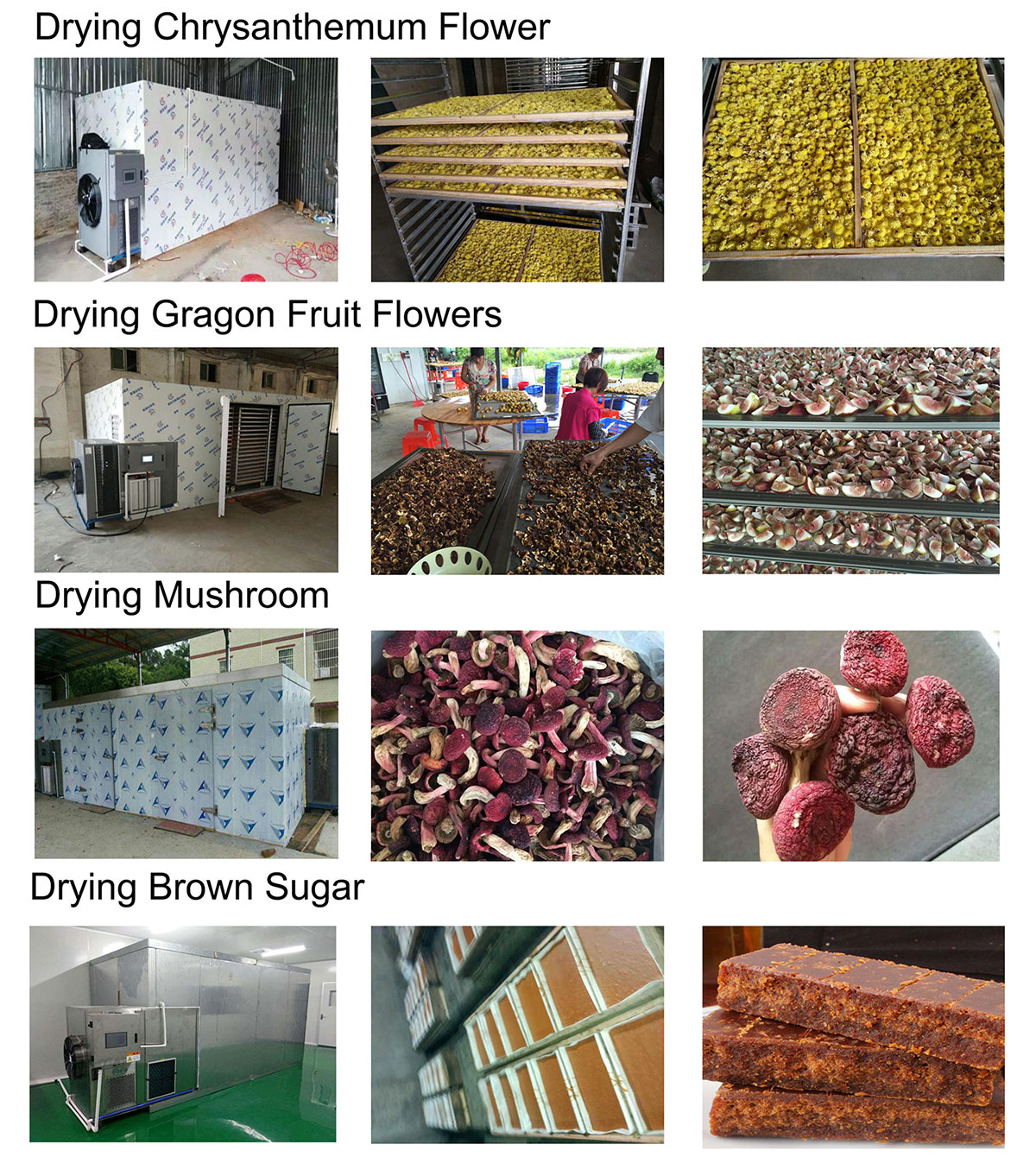

Our Factory:
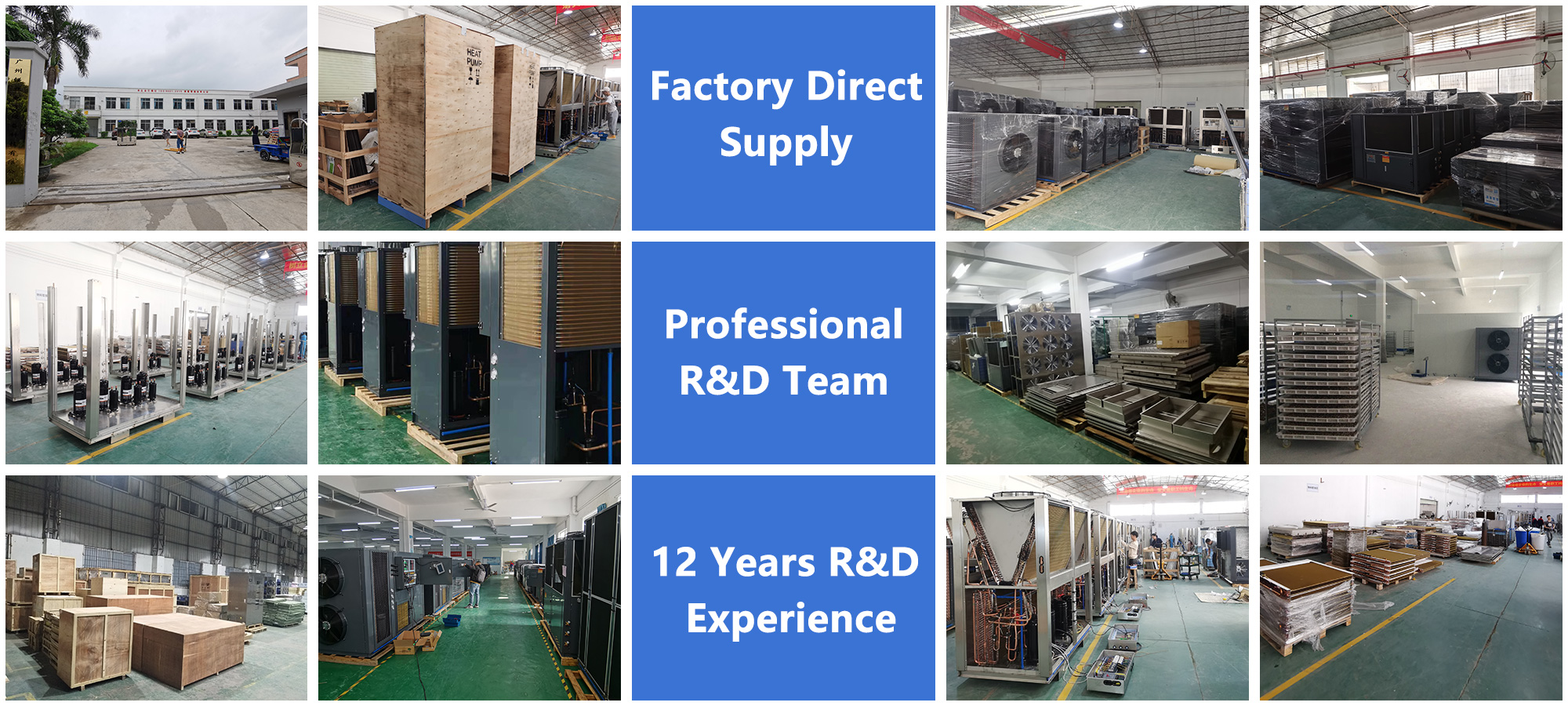
Production Processing:
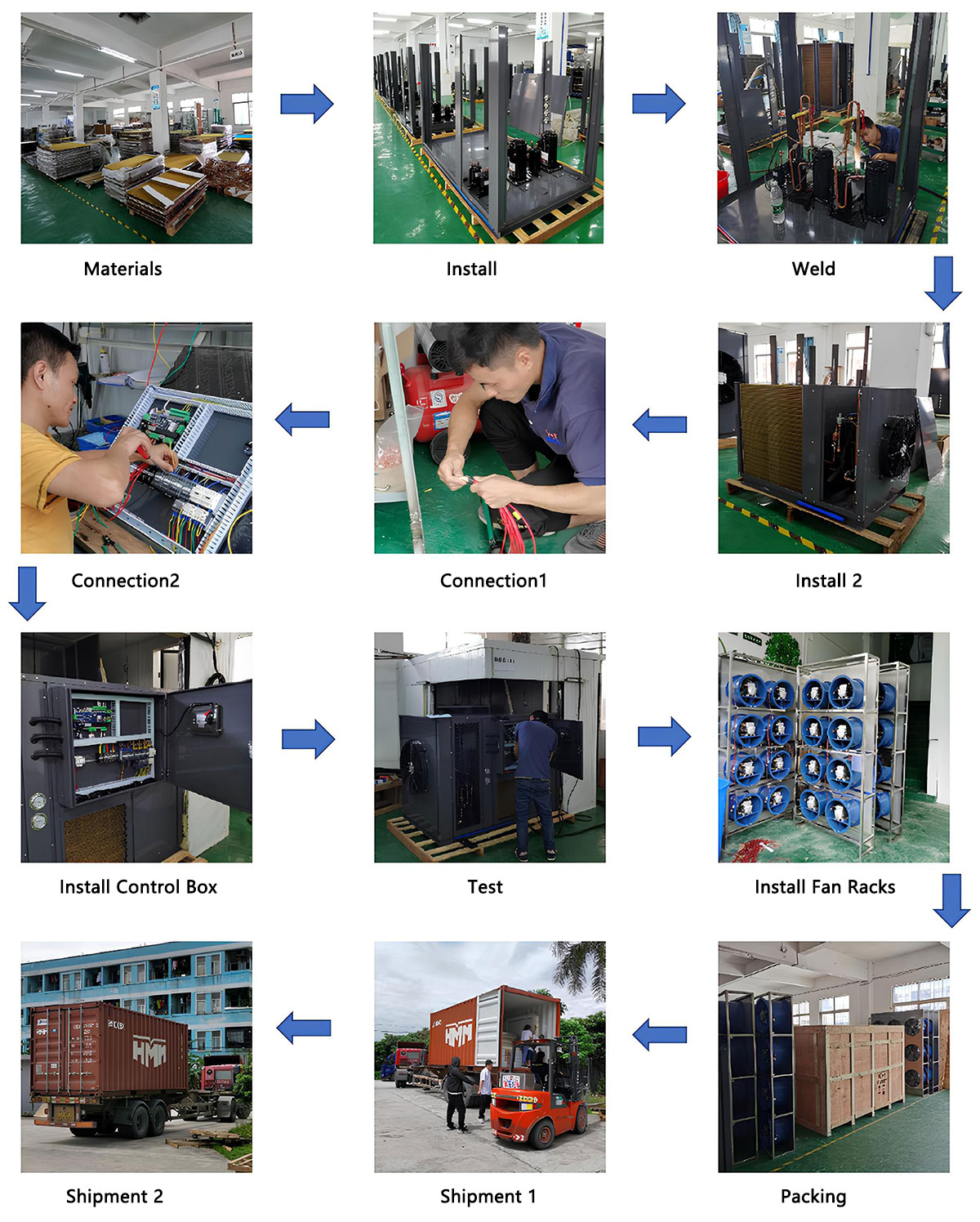
Drying Machine Components:
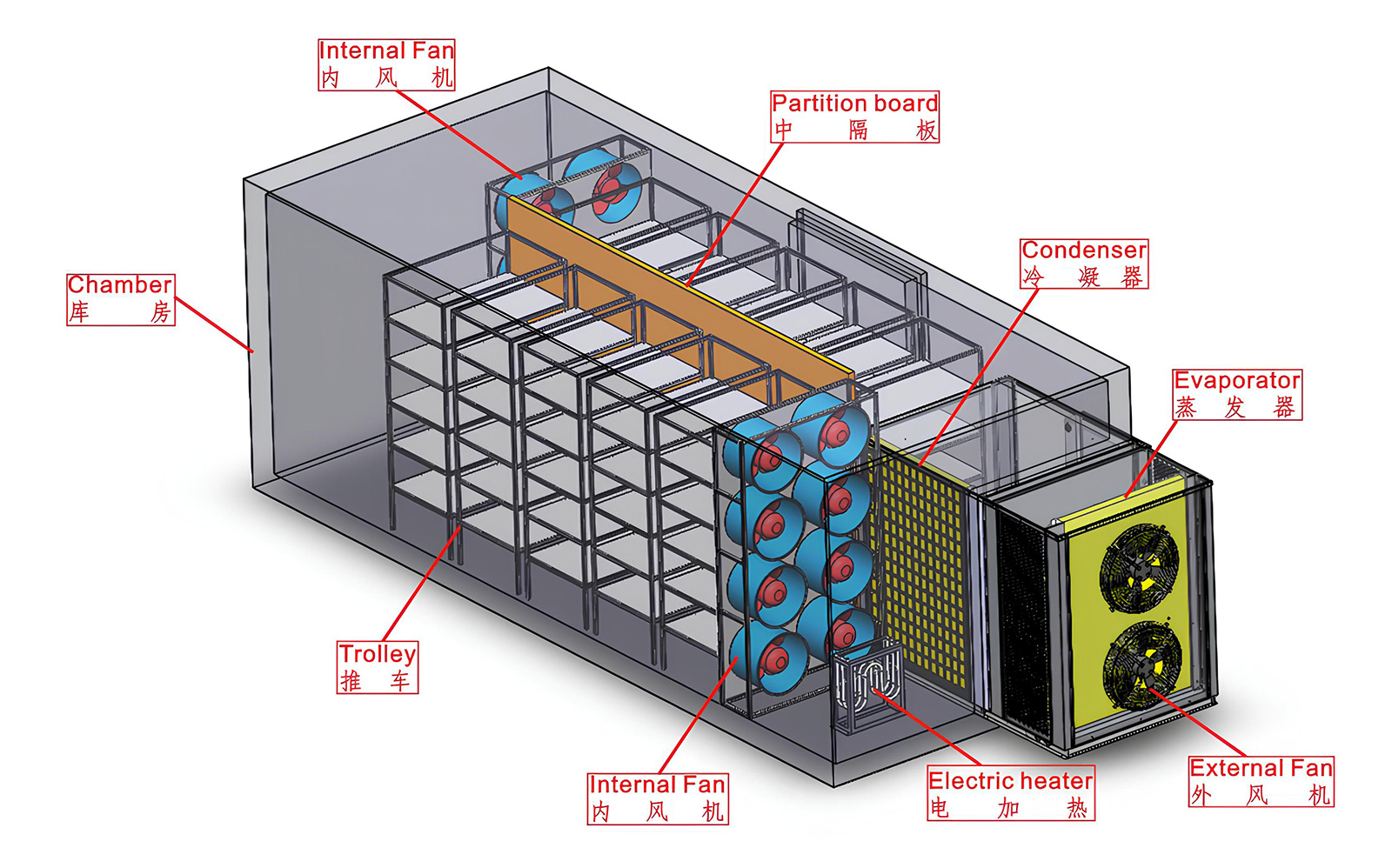
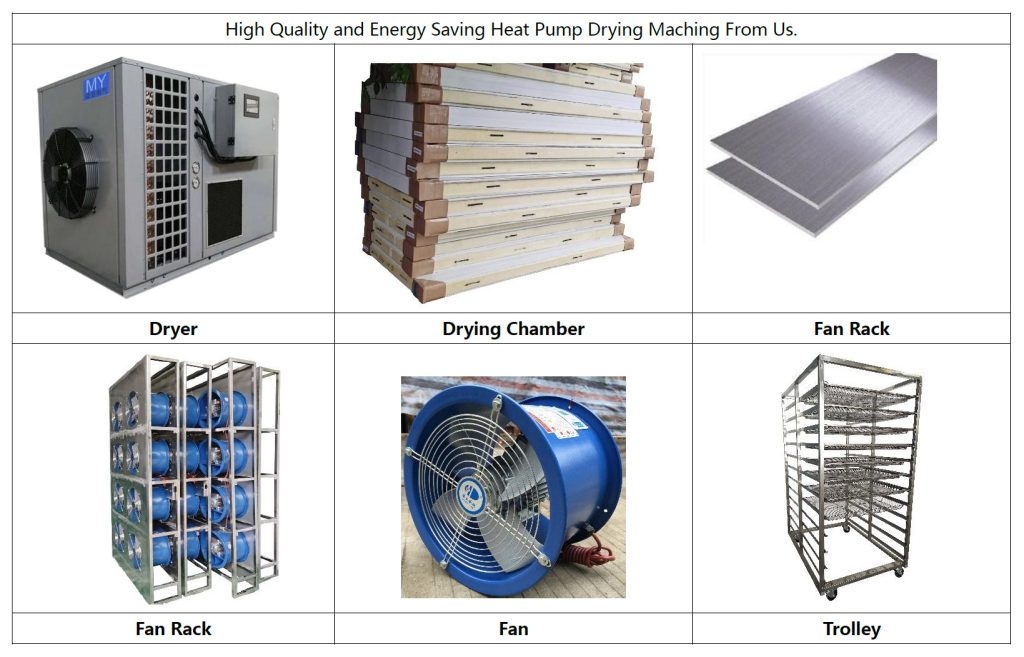
Standard Working Modes:
- Typically 3 modes available:
- Drying Only
- Rapid temperature rise; unable to discharge moist air
- Drying + Dehumidify
- Chamber temperature rises while discharging moist air
- Cooling
- Temperature can drop to 10°C (minimum)
- Important Note:
- If temperature control becomes unstable, switch to Temperature & Humidity Mode.
- Drying Only
Drying Machine Common Issues
- Q1: High Pressure Protection
- A1.1: Hot air circulation system failure
- AC contactor overload protection
- (Check phase loss/loose terminals/voltage instability)
- Partial fan failures
- (Verify switches configuration and burnt components)
- Mechanical fan damage
- (Replacement or removal required)
- AC contactor overload protection
- A1.2: Tray overloading phenomenon
- Optimal spacing: 8-10cm between trays
- (Causes airflow obstruction in drying chamber)
- Optimal spacing: 8-10cm between trays
- A1.3: Electronic expansion valve anomalies ▪ Automatic minimum aperture adjustment
- (Sensor calibration: Reposition or exchange Sensor 1/2) ▪ Valve body malfunction
- (Manual rotation intervention needed)
- (Sensor calibration: Reposition or exchange Sensor 1/2) ▪ Valve body malfunction
- A1.4: Chamber overheating condition
- (Temperature parameter adjustment solution)
- A1.5: Refrigerant specification error
- (High-temperature type gas recharge required)
- A1.1: Hot air circulation system failure
- Q2: Low Pressure Protection
- A2.1: Gas leakage scenario
- (Leak detection and repair protocol)
- A2.2: Extreme cold environment
- (Extended check intervals or R22/R417A refill)
- A2.3: Valve aperture deficiency
- (Expansion valve opening adjustment method)
- A2.1: Gas leakage scenario
- Q3: Exhaust Temperature Overload
- A3.1: Gas leakage recurrence
- (Refers to Q2.1 resolution process)
- A3.2: Valve operational failure
- (See A1.3.2 corrective action)
- A3.1: Gas leakage recurrence
- Q4: Sensor Malfunction
- A4.1: Temperature sensor defect
- (Replacement procedure guidelines)
- A4.1: Temperature sensor defect
- Q5: Moisture Evacuation Failure
- A5.1: Dehumidification fan damage
- A5.2: Control system malfunction
- A5.3: Power delivery irregularity
Our Services
A. Payment Service
- T/T (Telegraphic Transfer)
• Applicable to all transaction types. - L/C (Letter of Credit)
• Exclusively available for container orders. - Western Union
• Recommended for sample orders and spare parts procurement.
B. Technical Service
- Capacity Analysis & Model Recommendation
• We provide customized capacity calculations and optimal model selections based on operational requirements. - Professional Technical Support
• Comprehensive refrigeration and electronic engineering assistance for installation, debugging, and system operation. - Spare Parts & Post-Warranty Support
• Genuine spare parts and technical guidance provided during and after the warranty period. - Training Programs
• On-site or factory-based training courses available upon request.
C. After-Sales Service
- Technical Assistance
• Continuous support for installation, operation, and maintenance. - Warranty Policy
• 12-month warranty coverage with optional extension. - Cost-Effective Post-Warranty Support
• Spare parts and technical services offered at competitive rates after warranty expiration.